Stainless steel and aluminum alloy are most widely used in industry and domestic purposes.
Many things around you, from your house to your office, kitchenware to aircraft engineering, are made up of these metals.
Stainless steel and aluminum are very popular for their excellent lustrous appearance, Durability, strength, and corrosion resistance.
However, stainless steel is a hard, strong, and durable metal that is more difficult to deal with; on the other hand, aluminum is a soft, malleable, ductile, and lightweight metal.
Although aluminum alloy and stainless steel appear to be very similar, but there are some fundamental differences in their composition and mechanical properties.
In this article, we will discuss all the differences between aluminum and stainless steel in detail.

Stainless steel generally contains at least 11% chromium in its composition.
It is a ferrous metal with strong tensile strength and magnetic properties.
Stainless steel comes in several grades. A series number is assigned to each grade, along with a numerical grade.
The numbers differentiate steel grades based on composition, physical qualities, and applications. The 304 and 316 are the most commonly used grades of stainless steel.
What is Aluminum Alloy?
Aluminum is a silver-gray color lightweight metal that is more ductile and malleable than stainless steel.
It can be found in a variety of daily objects, including cans, foil, window frames, aviation parts, and automobile wheels.
Aluminum has numerous useful features, such as being strong but lightweight, corrosion-resistant, and nonmagnetic. It has better thermal and electrical conductivity than stainless steel.
Material Performance in Various Environments
Property | Stainless steel 316 (SS 316) | Aluminum 6061 (AL 6061) | Polycarbonate (Thermoplastic) |
Corrosion resistance | Excellent | Good Can be enhanced by anodizing | Poor |
Extreme temperature resistance | Good (-196°C to 870°C) | Moderate (-80°C to 200°C) | Good (-40°C to 130°C) |
Salt water performance | Very Good; <0.01 mm/year rate | Moderate; 0.1-0.9 mm/year rate | Poor |
Ultra violet radiation effect (UV) | Moderate; Requires coating | Poor; Requires coating | Good; UV-stabilized |
Alkali resistance | Good | Moderate | Good |
Acid resistance | Excellent for diluted acids. | Ineffective in strong acids. | Fair in weak acids |
Organic chemical resistance | Good; in oils/ solvents | Moderate; Varies with chemical | Excellent |
Humidity resistance | Very Good | Good | Excellent |
Under stress performance | High (yield strength ~205 MPa) | Medium (yield strength ~275 MPa) | Low (yield strength ~65 MPa) |
Strength And Durability Of Stainless Steel Vs Aluminum Alloy
Tensile Strength
Tensile strength is one of the important factors of any material, and it can be tested by the tensile testing machine. Stainless steel has better tensile strength than aluminum. The minimum tensile strength of stainless steel is 505 MPa, whereas aluminum has 110 MPa.
Fatigue Strength
The behavior of the material under repeated stress is called fatigue strength. For stainless steel, the fatigue strength is 250 MPa. In contrast, aluminum has a fatigue strength of 96.5 MPa.
Impact Resistance
Impact resistance is essential for safety. Because of its strong composition, stainless steel has a better resistance. Aluminum bends more easily, which allows it to absorb shocks better.
Wear Resistance
Wear resistance refers to a material’s resistance to volume loss caused by mechanical movements like rubbing, sliding, or scraping. Stainless steel performs well on the ASTM G65 test, with a rating ranging from 40 to 80 g. Aluminum has a higher wear rating, ranging from 150 to 250 g.
Compressive Strength
Compressive strength is described as a material’s resistance to breaking when compressed. Stainless steel can hold up to 220,000 psi. In contrast, aluminum has a maximum pressure of 70,000 psi.
Shear Strength
Shear strength is a material’s measurable capacity to withstand structural failure. Stainless steel tools and equipment withstand more cuts than aluminum, as most surgical tools and blades are constructed of stainless steel rather than aluminum. The shear strength of aluminum is 40,000 psi, but stainless steel has 70,000 psi.
Hardness
Stainless steel has better hardness than aluminum alloys due to its chemical structure. According to Rockwell Hardness tests, stainless steel can score up to 95Rb, while aluminum only gets 60Rb.
Modulus of Elasticity
The modulus of elasticity indicates the bending capabilities of materials. Aluminum has a modulus of 10,000 ksi, which is one-third that of stainless steel (28,000 ksi). This indicates that stainless steel has a higher modulus but less bending.
Yield Strength
Yield strength is the greatest stress a material can withstand before plastic deformation occurs. The yield strength values for stainless steel range from 30,000 to 90,000 psi, while aluminum is 40,000 psi.
Formability And Machinability Of Stainless Steel Vs Aluminum Alloy
Stainless Steel Formability
Stainless steel has good bending and shaping properties. One typical variety, 304 stainless steel, works well for forming. Also, experts recommend 316L for its great corrosion resistance.
Aluminum Formability
Aluminum is a preferable choice due to its lightweight and outstanding formability. The 3003 and 5052 alloys are still used for sheet metal. Furthermore, aluminum is exceptionally resistant to rust.
Stainless Steel Machinability
The stainless steel performs exceptionally well in cutting and drilling. Due to the addition of sulfur, grade 303 reigns supreme, and grade 416 stainless steel Is better for heavy-duty projects. Remember that high-speed steel (HSS) tools perform well on stainless steel.
Aluminum Machinability
Aluminum machining takes a different approach. Alloys such as 6061-T6 and 2024 cut very smoothly. Carbide tools penetrate aluminum sheets like a hot knife through butter. Even without decreasing fluids, heat remains low. Aluminum machining produces quick, rust-free parts for a wide range of applications.
Stainless Steel Weldability
Stainless steel has good weldability, with grade 316L showing superior weldability to others. The Electrode Inert Gas (TIG) method firmly connects steel parts. Finally, stainless steel provides corrosion-resistant welding, even in saltwater!
Aluminum Weldability
Aluminum alloys, particularly the 6061 alloy, have an outstanding welding class. Because the metal is only one-third the weight of stainless steel, it requires less energy, around 65 amps for 1/8″ thickness.
Bending Characteristics
When it comes to bending, stainless steel shows rigidity. For example, the 304 grade springs back around 3 degrees. In contrast, aluminum bends gracefully. Therefore, bending tools use less force to bend aluminum and its alloys.
Deep Drawing Capability
The 430 stainless steel, mostly used for deep drawing, has an ultimate tensile strength of 450 MPa. Stainless steel is used in this procedure to create durable kitchen sinks and pots. On the other hand, 3003 aluminum alloy has ductility and 130 MPa strength. Aluminum is quickly becoming a popular material for gasoline tanks and cookware.
Cutting Ease
Stainless steel resists cutting forces. The 440C grade is extremely hard and dulls cutting tools. High-speed steel blades become necessary for cutting this grade. Aluminum is easy to cut since it has a low tensile strength of 55 MPa.
Stainless Steel Vs Aluminum – Differences in Weldability
Melting Point
Stainless steel requires 2,550°F (1399 °C) to melt. In comparison, aluminum requires only 1,221°F (660 °C). Heating stainless steel in the manufacturing process requires more time and energy. So, aluminum is more cost-effective than steel during melting.
Thermal Conductivity
Aluminum has great thermal conductivity. Aluminum can transport heat at a rate of 250 W/mK. The value for stainless steel is significantly lower, at 16 W/mK.
Electrical Conductivity
Aluminum far surpasses steel in electrical conductivity. Aluminum has an electrical conductivity of 37.7 mS/m. Stainless steel falls behind at 1.45 MS/m. This makes aluminum more appropriate for electrical applications.
Weight
Aluminum is quite light in weight when compared to stainless steel. One cubic foot of aluminum weighs approximately 168.48 pounds, and stainless steel weighs 494.21 pounds. Aluminum alloys are mostly used in the aerospace industry for their lightweight and good strength, while steel is used to make heavy-duty bridges.
Corrosion Resistance
Stainless steel has at least 10.5% chromium, which acts as a rust-resistant barrier. Aluminum reacts with air to produce aluminum oxide. As a result, aluminum is also resistant to rust.
However, in salty conditions, stainless steel outperforms aluminum regarding corrosion resistance.
Welding Techniques
Stainless steel melts at approximately 2,500 °F. In comparison, aluminum melts at 1,221°F. As a result, aluminum requires less heat in welding. Both the TIG and MIG welding processes are suitable for aluminum. On the other hand, stainless steel prefers Arc and spot welding.
Weld Joint Preparation
The preparation of aluminum weld joints requires more attention. The oxide on aluminum melts around 3,700°F, which is substantially higher than the aluminum itself. For stainless steel, ensure the surface is clear of impurities like grease. Welds are stronger when the surface of the stainless steel is cleaned.
Weld Appearance
After completing the welding check, the finished weld. Aluminum welds may appear dull and unappealing. In contrast, stainless steel welds have a bright and clean appearance.
Cost
Aluminum is very cost-effective in any project due to the abundance of raw materials, while stainless steel is a pricey option due to its composition.
Weight and Density Comparison
Density of Stainless Steel
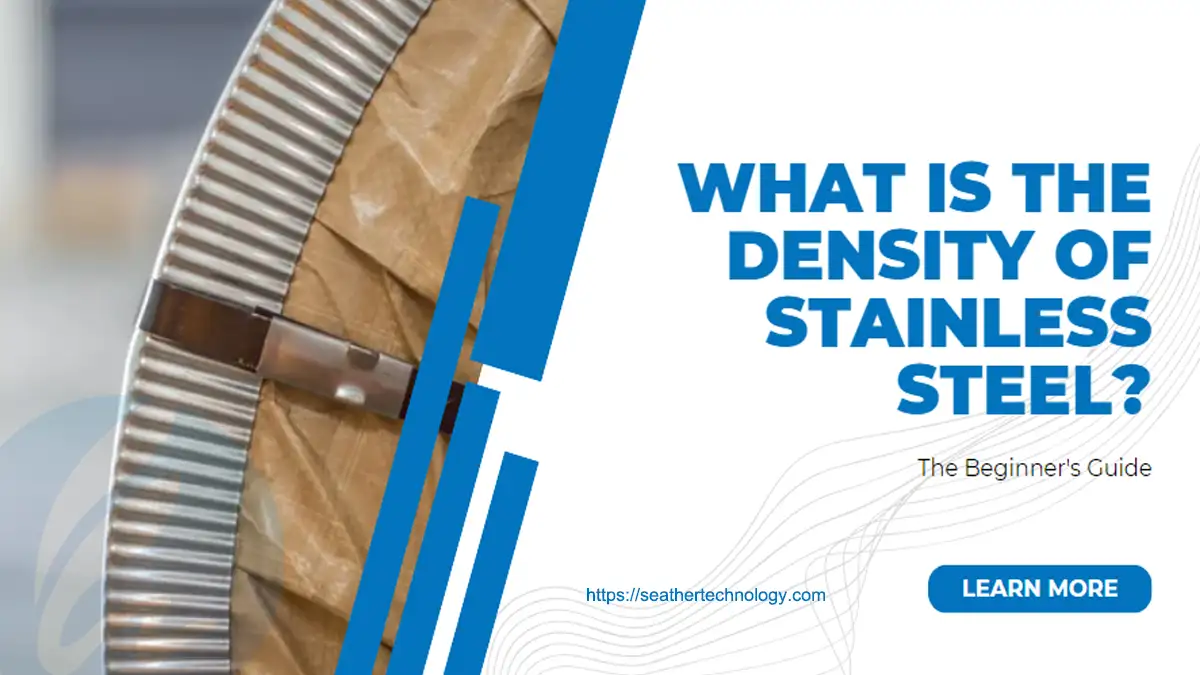
The density of stainless steel is much higher than that of aluminum alloys. Its density is around 8,000kg/m3. For example, if you fill a one-meter box with stainless steel, you’ll be dealing with a weight nearing 8000 kg.
Density of Aluminum

As we discussed, aluminum is light in weight; hence, its density is lower than steel.
Within the same cubic meter, there are only roughly 2700 kilos of aluminum.
The density of aluminum is approximately 2,710kg/m3. Nonetheless, a lower density frequently equals less strength; therefore, aluminum may not be the best option when high strength is required.
Applications and Industries
Construction industry
Stainless steel and aluminum are mostly used in the construction industries. Grade 304s of stainless steel is used in building materials, and aluminum is used for making frames for windows.
Automotive industry
Stainless steel is used for making automotive parts like exhausts and rims, while aluminum is used for making engine parts and panels.
Aerospace industry
Aircraft prefer lightweight materials. Aluminum grade AL-7075 or 7050 is most commonly used to manufacture aircraft structural parts. On the other hand, SS-316 is ideal for airplane landing gear.
Kitchenware
Stainless steel and aluminum are most commonly used in making kitchenware. When it comes to nonstick performance, the decision between hard anodized aluminum and stainless steel cookware becomes critical. Stainless steel cookware is quite durable. Aluminum heats up quickly due to excellent thermal conductivity.
Conclusion
In conclusion, both of these metals are very popular due to their unique properties.
Stainless steel is known for its strength, durability, and corrosion resistance, whereas aluminum is popular for its ductility and thermal and electrical conductivity.
Contact us for further guidance regarding your stainless steel and aluminum project. We have many years of experience dealing with these alloys.